BMW’den yapılan basın açıklamasına göre seri olarak üretilen ilk BMW i4, Münih BMW Group Fabrikası’ndaki üretim hatlarından çıktı. Şirketin ana fabrikası artık tüm tahrik çeşitlerini tek bir montaj hattında üretiyor. BMW AG Üretimden Sorumlu Yönetim Kurulu Üyesi Milan Nedeljković, “Tesis ve ekip için BMW i4’ün piyasaya sürülmesi elektrikli mobiliteye giden yolda bir kilometre taşıdır” dedi. “2023 yılına kadar Münih tesisimizde bulunan tüm araçların yarısından fazlası elektrikli bir sürüşe sahip olacak. Çoğunluk tamamen elektrikli olacak, böylece Münih tamamen elektrikli oluyor.”
Neredeyse 100 yıllık fabrikanın sınırları içinde tamamen elektrikli BMW i4’ün üretimini kurarken, sistemlerin dönüştürülmesi ve kurulumu özellikle zorlayıcı olduğu belirtildi. Münih BMW Group Fabrikası Direktörü Peter Weber, “Yeni aracı üretimi durdurmadan mevcut sistemlerimize entegre etmeyi başardık. Ekip ve ortaklarımız harika bir iş çıkardı. Alan kısıtlamalarına rağmen, mevcut sistemler kaldırıldı, yenileri kuruldu ve üretim kapasitesi arttırıldı.” dedi.
BMW Group, Münih Fabrikasını elektromobilite için yenileme planlarını ilk olarak bir yıldan kısa bir süre önce duyurmuştu: Yeni araç montaj ve karoser tesisleri inşa edilecek ve motor üretimi, üretim ağının diğer bölümlerine taşınacaktı. O zamandan beri yüzlerce çalışan başka teknolojilerde veya başka tesislerde çalışmaya başladı. Bu yılın sonunda, dört silindirli motor üretimi Hams Hall, İngiltere ve Steyr, Avusturya’ya taşınacak. Motor üretiminin bir bütün olarak Münih’ten taşınmasının ise en geç 2024 yılına kadar tamamlanacağı öngörülüyor.
Elektromobiliteyi seri üretime entegre etme
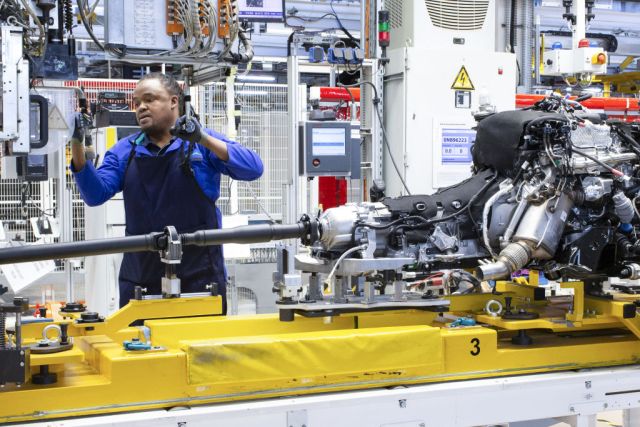
BMW i4 ile geleneksel mimariler arasındaki temel fark, elektrikli tahrik ve batarya sistemidir. Münih üretim hattındaki mevcut sistemlerin yaklaşık yüzde 90’ı yeni model için kullanılabilir durumdayken sadece zemin montajı ve arka uç için ilaveler eklendiği belirtildi.
Bir başka oldukça karmaşık konu, yüksek voltajlı pilin montajına entegrasyonunda yaşanmış. Pil takımı alttan çalışan yeni, tam otomatik bir pil montaj sistemi ile gövdeye vidalanmıştır. Montaj öncesi tam otomatik, yüksek çözünürlüklü kamera sistemleri, yüzey taraması yaparak yüzeyin kesinlikle temiz olduğundan ve hasara neden olabilecek herhangi bir kirlilik bulunmadığını garanti etmektedir.
BMW Group’un ana fabrikası artık yalnızca BMW i4’ü değil, aynı zamanda içten yanmalı ve hibrit BMW 3 Serisi Sedan ve Touring, BMW M3 ve BMW 4 Serisi Gran Coupe’den oluşan kapsamlı bir ürün portföyü üretiyor.
BMW’de dijitalleşme son hız devam ediyor
Artan dijitalleşme, BMW Group üretiminde önemli bir rol oynuyor. Münih Fabrikasının tamamı şu anda hem binanın hem de sistemlerinin eksiksiz bir temel dijital veri setini elde etmek için en ince ayrıntısına kadar 3D olarak taranıyor. Taramalar daha sonra işlenip, buluta kaydediliyor. Böylece verilere sezgisel, tarayıcı tabanlı bir araç kullanılarak her yerden erişilebilir hale getiriliyor. Spartanburg ve Regensburg da dahil olmak üzere birçok tesis zaten tamamen 3D tarandı ve Dingolfing Tesisi şu anda tarama sürecinden geçiyor. 2022’nin sonunda, BMW Group üretim ağındaki tüm büyük otomobil fabrikalarının yapısı taranmış olacak ve dijital veriler herkesin kullanımına sunulacak.
BMW Group, bugün binaları ve sistemleri planlamak için sanal planlama araçlarını kullanıyor. Örneğin, BMW i4 için aks ön montajı NVIDIA tarafından Omniverse Nucleus platformuyla planlandı. Bu, tek bir işbirliği ortamında gerçek zamanlı simülasyonlar oluşturmak için çeşitli üreticilerin tasarım ve planlama araçlarından gelen verileri birleştirir. 3D taramalardan elde edilen veriler de Omniverse platformuna aktarılır.
Diğer dijital uygulamalar doğrudan üretimde kullanılmaktadır. Örneğin, radyo frekansı tanımlama (RFID), parçaların değer zinciri boyunca temassız ve otomatik olarak tanımlanmasına ve atanmasına olanak tanıyarak manuel tarama ihtiyacını ortadan kaldırır ve doğru arabaya doğru parçanın takılmasını sağlar. RFID teknolojisi koltuk üretiminde zaten kullanılmaktadır, ancak Münih Fabrikasında araç montajının çeşitli alanlarına da girmiştir. Bunun için gerekli olan akıllı etiketler, henüz tedarikçilerdeyken veya BMW Group bileşen üretiminde, montajda kullanıma hazır haldeyken parçalara yapıştırılır. Daha sonra, her arabadaki etiketli her bileşeni izleyen hat tarafındaki antenler tarafından alınırlar. Uygulanan dijitalleşme çalışmalarını ile amaç, süreçleri daha hızlı ve daha güvenli hale getirirken, verimlilik ve kaliteyi arttırmak.
Ters Osmoz sistemi, su tüketimini 6 milyon litre azaltacak
Üretim sistemi içinde, sürdürülebilirlik konusu temel bir öneme sahiptir. BMW, CO2 emisyonlarını azaltmak ve kaynak kullanımını en aza indirmek için bütünsel bir yaklaşım benimsemiştir. 2006 ile 2020 arasında, üretilen araba başına kaynak tüketimi yarıdan fazla düştü ve CO2 emisyonları %78 oranında azaldı. Amaç, 2030 yılına kadar üretilen araç başına CO2 emisyonlarını %80 daha azaltmak. Münih Fabrikasında bazı değişiklikler yapıldı ve bir dizi yeni önlem uygulandı. Bu nedenle tesis artık tatlı su tüketimini azaltmak için ters osmoz sistemini kullanıyor. Sistem, bu yılın ilkbaharında üretime entegre edildi. Yeni sistemin toplam yıllık tatlı su tüketimini 6 milyon litreden fazla azaltması bekleniyor. 1997’den beri BMW Group Münih Fabrikası, fabrika kampüsünde kendi kaynağından gelen yeraltı suyunu kullanıyor. Bu, tesisin yıllık ihtiyacının yaklaşık yarısını karşılamaya yetecek kadarını sağlar ve değerli içme suyu tasarrufuna önemli bir katkıda bulunur.
Yeni sürdürülebilirlik hedefi: Ulaşım lojistiğinde sıfır yerel emisyon
Özellikle CO2 emisyonlarını azaltmaya odaklanan BMW Group, BMW i4’ün üretim lansmanı ile aynı zamana denk gelecek başka bir hedef daha duyurdu: “Önümüzdeki birkaç yıl içinde Münih Fabrikasındaki nakliye lojistiğinden kaynaklanan yerel emisyonlar kademeli olarak sıfıra düşecek.” Bu hedefin demiryolu taşımacılığı ve elektrikli kamyonların daha fazla kullanılmasıyla sağlanması beklenmektedir. Şu anda parça teslimatı için günlük 750’den fazla kamyon teslimatı gerekiyor. Gelecekte bu yolculukların şehir içi bölümleri elektrikli kamyonlarla yapılacak. Ayrıca Münih fabrikasından trenle ayrılan araçların payı şu an ki oran olan %50’den kademeli olarak arttırılacak.
Nihai amaç, Münih bölgesindeki nakliye lojistiğinden kaynaklanan emisyonları tamamen ortadan kaldırmaktır.
Münih BMW Group Fabrikası Direktörü Peter Weber: “Üretim tesisimizin şehirdeki konumu nedeniyle özel bir sorumluluğumuz olduğunun farkındayız. Kendi fabrikamızda CO2 emisyonlarını azaltma projemiz hem çevre hem de yakın çevremiz için olumlu olan büyük bir etkiye sahip olacak.”
Geçen yıldan bu yana, BMW Group tarafından dünya çapında sağlanan tüm enerji yeşildi. Örneğin BMW i4’ün üretimi için, yeşil enerjinin çevresel referansları, doğrudan bölgesel hidroelektrik santrallerinden tedarik edilerek daha da geliştirildi. Ayrıca, bu yıldan itibaren BMW Group, üretimden kaynaklanan kalan (Kapsam 1 + 2) CO2 emisyonlarını dengeliyor. Bunlar, birleşik ısı ve elektrik üretiminden kaynaklanır ve dünya çapında ilgili karbon kredileriyle tamamen dengelendiği belirtilmektedir.